

From the observations made, phenomenological models are proposed to describe the initial micro crack formation considering the shock wave and thermal influence caused by the laser pulses.
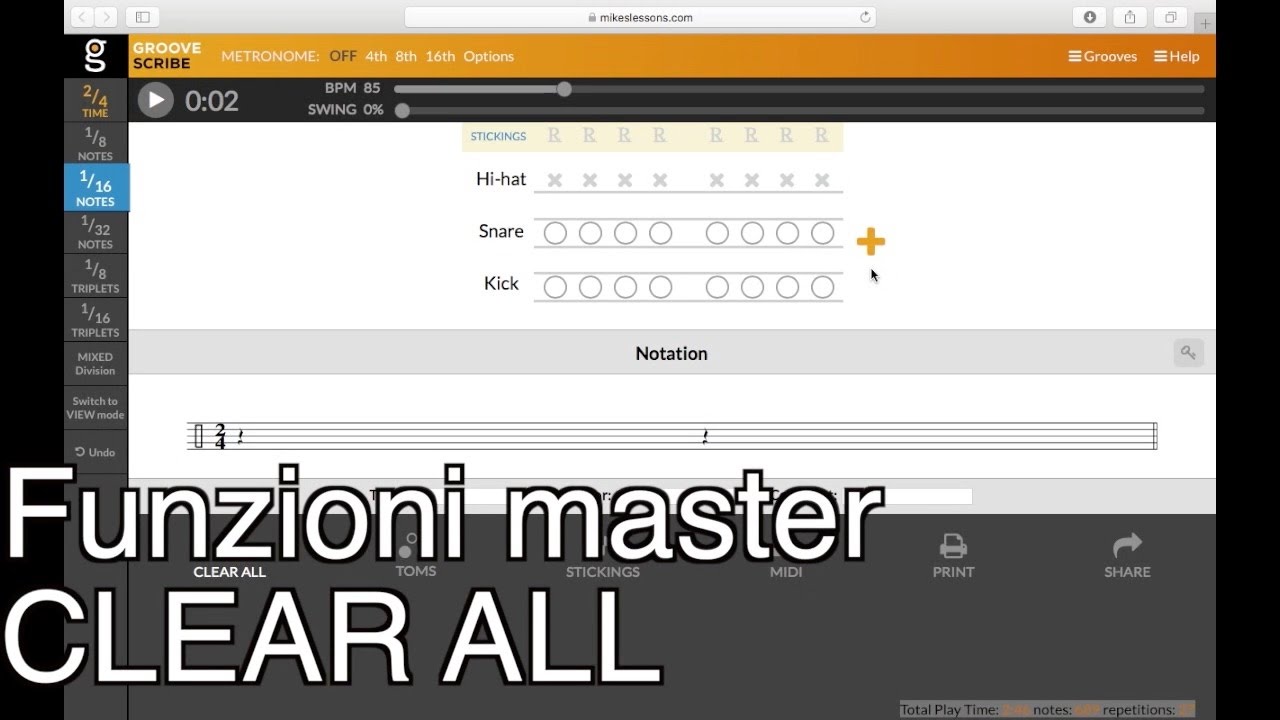
Photoelastic measurements were done to assess the stress distribution within the glass and show cumulative interactions at the filament extremity. The filaments and cut edge are analyzed with scanning electron- and laser scanning microscopy to study the topological phenomena and roughness. In this study, we utilized a Nd:YAG laser with an average power of 100 W, a center wavelength of 1,064 nm, and a pulse duration of 12 ps via a specially designed optic to generate laser filamentation in soda-lime- and borosilicate glass with varying Pitch and Burst parameters. However, despite the large interest in the laser/glass interaction for various laser sources and pulse durations, the process of cleaving and the underlying mechanisms are fairly undescribed.
GROOVE SCRIBE DOWNLOAD FREE
In comparison with other techniques the superior benefits are a small heat-affected zone, a quasi-non-gap cut, and the possibility to free from cut. Utilizing ultra-short-pulse laser filamentation of glass is one of the latest developed techniques to cut glass. At 15.5 W, the ablation efficiency and effective cutting speed per incident laser power increased by 16% and 22%, respectively, compared with cutting in water in a low-laser-power regime.

Cutting in a high-laser-power regime was only carried out in water. Glass strips cut in water in the low-laser-power regime had the highest characteristic strength of 117.6 and 107.3 MPa for the front and back sides, respectively. Transition to smaller hatch values improved the cut sidewall quality by suppressing the ridge formation, but negatively affected the ablation efficiency and overall strength of glass strips. At optimal cutting parameters, ablation efficiency and cutting rates were the highest but cut sidewalls were covered with periodically recurring ridges.
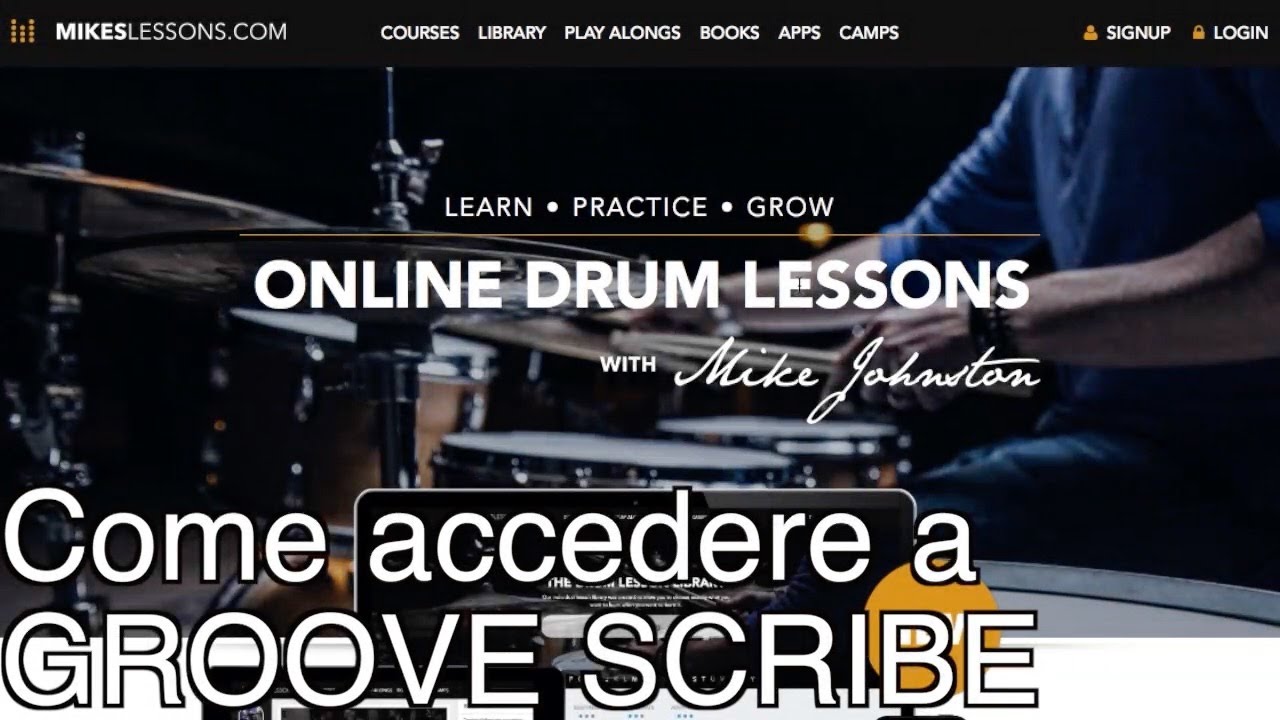
Thorough attention was paid to the effect of the hatch distance on the cutting quality and characteristic strength of glass strips cut in both environments. Low (2.1–2.75 W) and high (15.5 W) average laser power cutting regimes were studied. In this study, the cutting of borosilicate glass plates in ambient air and water with a 355 nm wavelength picosecond laser was carried out. However, the author 20 did not mention the mechanical frac- turing system that was used to separate the samples along the scribe. However, the power densities must be selected carefully to effectively evaporate without causing large amount of melting. It was found that a pulsed laser gives better results than CO 2 laser in scribing operation because it generates higher peak powers which evaporates more material and gives less time for the absorbed energy to be conducted. CO 2 laser with a wavelength of 10.6 lm was found to be ideal for scribing most nonmetals. 27 Lumley 20 demonstrated the use of CO 2 and Nd:YAG lasers for laser scribing. Several patents for laser scribing are available such as Patel and Baker 26 and Wills et al. Therefore, finishing processes are required, which add extra cost to the manufacturer. 25 The scribing process incurs damage to the cut edge which can also cause damage to the glass surface. In the second stage, breaking by applying a mechanical force takes place normally with the help of vacuum chucks or by crack rollers. It is necessary to con- centrate the laser energy on a narrow line with the workpiece in the focal plane. In the first stage, partially penetrating holes, a groove or deep vents at depths of one third to one half of the material thickness, are produced using a laser. The process is shown schematically in Fig. 19 Laser scribing is a two stage process and is quite similar to traditional mechanical scribe and break method. scribing for brittle materials was originally pro- posed by Garibotti.
